Top 10 Tips on Using FEA within AIP
Simulation Suite
- Try to avoid applying loads on
points or small edges as these will cause non convergence of results
due to very high localized stresses.
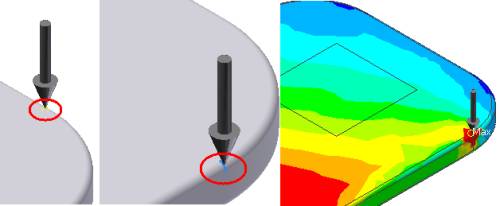
- Try to avoid applying constraints
on points or small edges as these will cause non convergence of results
due to very high localized stresses.
- There are 3 elements used within
AIP including Brick, Tetrahedon (Tet) and Shells.
- Brick elements require fewer
elements than Tetrahedon elements to get accurate results. Note Brick
elements are only used by the software for simple shape components
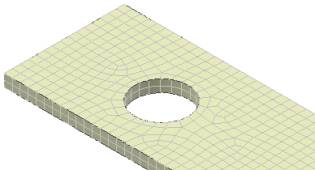
- Tetrahedons are the default
elements as they have the ability to mesh more complicated components
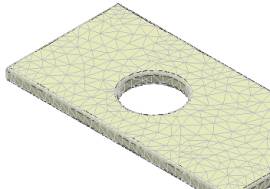
Note: By simply adding fillets the
mesher uses Tetrahedons instead of Brick Elements.
- Shell elements are more accurate
than both Brick and Tet elements for thin components like Sheet metal
parts.
Note Using shell element will speed up the analysis time when
compared to using Solid Tetrahedon elements.
- The deformation results are not
affected by using a finer mesh or lower mesh relevance.
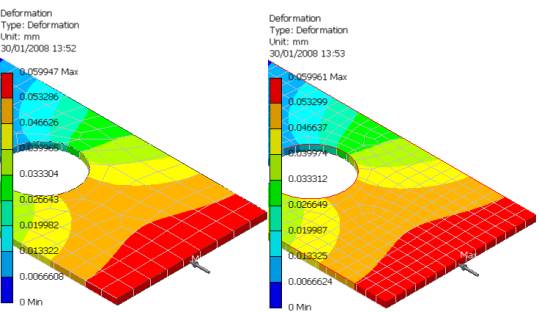
Note: The analysis
calculation will be quicker using a lower mesh relevance.
- You can use the Spit feature
command to define the precise location and size of a face to which you
can apply a load or constraint. This method is better than creating
dummy features, to which loads can be applied, as it avoids potential
high localized stresses.
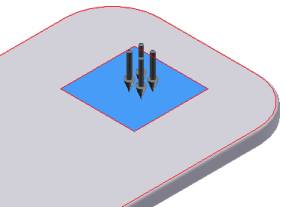
- If you have an assembly made
of the same material you can use the derived feature command to convert
the assembly to a single component. This will then allow you analyse
your component.
Note:
- This method will not allow you
to determine the contact stresses between components.
- Make sure you fill any gaps
between components, to avoid any mesh errors.
- Results below a Factor of Safety
of 1 are not valid. So always make sure the Factor of Safety plot shows
all values above 1.
- Always suppress Design Features
that are not part of the structural integrity of the component. This
will also help to speed up your analysis time and avoid possible mesh
errors, in addition to high localized stress problems.

Note: Its easier to suppress features
within the stress analysis environment
-
Deformation values should always
be small in relation to the overall size of the component. If you
expect larger deformations then you need to conduct a non-linear analysis.
- Use frictional constraints to model
Quarter models.
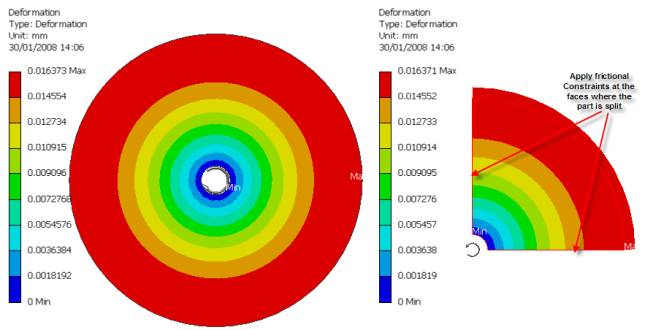
Note: A quarter model will achieve
the same results, with using fewer elements.
For further tips & tutorials visit
www.vdssolutions.co.uk
wasim@vdssolutions.co.uk
Wasim YounisVDS Solutions Ltd
|